The Nissan Deltawing finally got a chance to prove itself two weeks ago coming in fifth at the Petit Le Mans at Road Atlanta. The car survived two collisions, one at Le Mans and one during practice for Petit Le Mans, before finally getting a chance to finish a race and showing the world what it could do.
The entire Deltawing concept has revolutionized how people think of race cars. The car has proven that it has competitive speed while using half the power, fuel and tires thanks to greatly reduced aerodynamic drag and a well thought out design. Now we get the privilege to see how it drives and to understand the engineering that makes it work up close thanks to Chris Harris and the DRIVE channel. Harris takes the car around Road Atlanta for 5 laps to get a feel for its character before having the its creator, Ben Bowlby, guide him through the suspension systems. They touch on a few interesting engineering concepts. Watch the video and we’ll talk about them afterwards.
The key to understanding how the Deltawing is able to function is to realize that most of the weight sits on the massive rear tires. 72.5% of the car’s weight and 76% of its aerodynamic drag force is supported by the rear axle. That’s why Bowlby was able to pick up the nose of the car by himself so easily. This also means that most of wheelbase is a lever for the front tires to act on the car’s center of mass. The rear tires end up doing more than half of the braking and the torque vectoring of the differential also helps with the steering. The pounds per square inch of tire contact patch of the front and rear end up being pretty similar even though the front tires are so narrow.
When Bowlby mentions “scrub drag,” I believe he is talking about the torque it takes to rotate a front tire with the steering. Pretend we’re looking down at a tire from directly above it. Lets say the tire’s contact patch with the ground is a circle. When the tire is turned for steering, this circle has to rotate. At the center of the circle, you get perfect rotation without displacement. As you move away from the center of the contact patch, the tread is having to move across the road surface as the tire rotates. This is what is known as “scrub” and it’s what makes it hard to turn the steering wheel of your car when it’s stationary. Modern power steering makes it so you don’t notice the effort, but you can hear the tires scrubbing when you do a 3 point turn. Since the Deltawing has such narrow front tires, there is a negligible amount of scrub when they are rotated. The two front tires scrub less than if their widths had been combined into a larger single tire. The result is less stress on the front contact patches from steering torque. Less stress means less chance of understeer which is why Bowlby says the front tires are being used more efficiently.
The rear suspension discussion was the part of the video that I found the most interesting. The rear wheels are connected to their springs and dampers with pushrods and rocker arms:
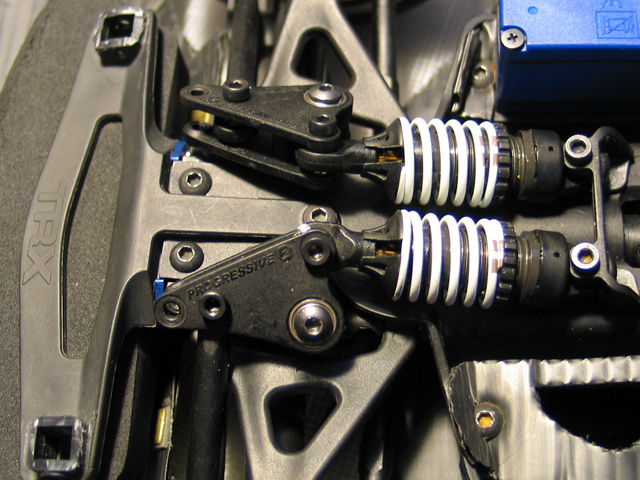
Push Rod Suspension Example via Traxxas.com – New holes were drilled in these rockers to mount the wheel’s pushrods closer to the pivot in order to reduce the leverage ratio.
Using the rocker arms gives the suspension a leverage ratio. This works just like what we were talking about with the circular tire contact patch. The further the pushrod is mounted from the rocker arm pivot, the more it moves when the rocker rotates. You can manipulate the lever lengths to change how much the shock compresses for how much the wheel moves.
The interesting part about the Deltawing is that they also used the rocker arms to amplify the effectiveness of the anti-roll bar. The anti-roll bar ties the suspension from each side of the car together so that they can’t have a large difference in ride height (compressed on one side and extended on the other). Check out our article on anti-roll bar tuning for the full explanation on how they work. Bowlby had to give the rear anti-roll bar a leverage ratio because the front axle of the Deltawing is too narrow to help control its body roll leaving the rear axle to pull double duty. Using traditional methods would have required rear springs that would have been too stiff for absorbing bumps (or “heave” as Bowlby calls it). Tying into the rocker arm system provides a pretty elegant solution to the problem of having massively disproportionate bump and roll requirements.
I have to admit that my initial impression of the Nissan Deltawing was that it was an idealistic engineering exercise that wouldn’t work in the real world. Bowlby and his team have proved me dead wrong. The car has excelled spectacularly in showing the world that environmentally responsible racing doesn’t have to be boring. All it takes is a willingness to think outside of the extremely well established box and perseverance. Lets hope more racing teams and sanctioning bodies took notice so we can see more cars like the Deltawing. Racing has always led to real world innovation and it should be no different when it comes to green car technology.
Sources: Nissan Newsroom, DRIVE and DeltaWing Race Cars
Pingback: Nissan ZEOD RC | FluxAuto
Pingback: Building the Nissan ZEOD RC – Chapter 1 | FluxAuto