In the second part of our discussion on why we should build electric cars, we’re going to take a closer look at what it takes to use a combustion engine and where electric motors can improve on their performance. Much of the technology required for the use of engines is accepted simply because it’s the way we’ve done it for a long time. Take a minute to give this question some serious thought: What if the car had been invented today? Given what you now know about where we get our oil (covered in Part I), do you think the established automotive industry would look the same if was built from scratch right now? Let me show you some of the facts.
This one will probably surprise you. Your typical car engine achieves about 18-25% efficiency. That’s it. Only one quarter of the energy that is contained in the gasoline that you purchase actually goes to turning the crankshaft of your engine. Where does the other 80% of the energy go? Heat and friction. Gasoline contains so much energy that we’re still able to power our cars with it even though engines are so inefficient. Here’s another way to look at it: 75% of your gas money is just being thrown away.
Electric Motor
Brushed DC motors like the ones found in forklifts and the one I’ll be using for the RX-8 Conversion run at about 85% efficiency. State of the art high voltage permanent magnet AC motors operate at 95-98% efficiency. That means almost all of the electrical energy provided to the motor turns into motion. One gallon of gas contains 33.7 kilowatt-hours of energy. The rule of thumb for electric cars is that the amount of electrical energy to give you the range of one gallon of gasoline is 8-10 kwh. That’s why electric cars are given such high “miles per gallon gasoline equivalent” ratings by the EPA.
With almost 75% of the energy of your gasoline being turned into heat, cooling is an essential part of any engine. Coolant has to be continuously pumped through the engine block and head(s) to prevent the parts from warping, seizing and cracking once the engine has reached operating temperatures. A thermostat has to be used to close the cooling circuit while the engine is warming up so that it doesn’t operate cold. A cold
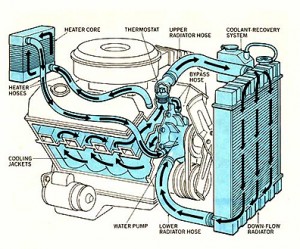
Electric Motor
Electric motors, their controllers and battery packs do require cooling, but not to the same extent as a combustion engine. Air cooling is sufficient for a lot of applications. Liquid cooling is used for heavy duty and high power applications, but much less is needed when compared to a combustion engine. The coolant also lasts longer because it doesn’t go through as harsh of a heat cycle when cooling an electric motor and its systems.
Your engine sees a lot of friction and stress during its normal use. The internal components see tremendous forces as they transform the linear motion of the pistons to the circular motion of the crank. Oil is the key component of the journal bearings on
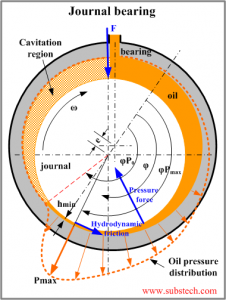
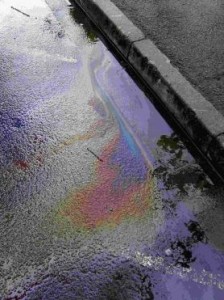
Electric Motor
Electric motors have one moving part, known as the stator, which uses traditional ball or needle bearings. These bearings have a long service life since the stator’s motion is a pure spin without much vibration and because they are not exposed the intense heat found inside of an engine.
When the power rating of an engine is given, it is a peak power figure that was achieved at high rpm and wide open throttle. The power delivery of the engine climbs a hill to get to that peak power number. Output is directly related to how fast the engine is turning. You can think of a combustion engine is an air pump. The faster it turns the more air it pumps through it. Moving more air through the engine means more fuel can be burned and more power can be made. The problem is that at low engine speeds and under heavy loads, the engine is not operating in optimum conditions. That’s why we have to pair engines up with multi-speed transmissions with clutches.
Electric Motor
The power output of an electric motor is dependent on how much current and voltage is being supplied to it. The current the motor sees is driver controlled through the throttle in an electric car. Full torque is available at all motor speeds starting at 0 rpm. The driver ultimately has more precise control of the power output since it doesn’t surge like it does in a combustion engine. On the drive train side of things, the transmission has to be more robust but needs less gears. Some electric cars are even direct drive without a transmission. That’s how the Tesla Roadster is set up.
It can be said that your engine is only as good as the machine shop that prepares it. There are hundreds of moving parts and fasteners inside of an internal combustion engine. All of these parts have to work in harmony when the engine is cold and after they’ve undergone thermal expansion as the engine warms up. All of the rotating parts

Electric Motor
The electric motor has a single moving part. Its complexity lies in the controllers (DC) and inverters (AC) that supply it with current and voltage. AC motors are the more intricate of the two with the inverter having to manage three phases of alternating current. Though complex, AC motors are capable of regenerative braking and higher efficiencies. High voltage wiring, fuses, shunts and contactors (relays) have to be used throughout an electric car to connect the battery pack with the motor. Special labeling and emergency disconnects must be used with anything involving high voltage. The battery pack also requires a computer management system to maintain cell balance and to prevent overcharging and overdischarging.
Combustion engines are a viable technology today because we’ve been producing them for hundreds of years. They were an obvious choice when other forms of technology couldn’t even think of rivaling the energy capacity of gasoline. Those circumstances have changed. We now have more cars than we can supply oil for or properly clean up after. More importantly, alternate technologies like electric motors are viable options with vast improvements on the combustion engine’s weaknesses. That makes me believe that if the car were indeed to be invented today, electric power would be the core of the automotive industry. That means there’s a disparity between where the technology should be and where it is right now.
Pingback: Why Build an Electric Car? Part 3: Nissan Leaf and Chevrolet Volt | FluxAuto